Austenitic stainless steel
Osprey® 904L
Osprey® 904L is a high-alloy austenitic stainless steel characterized by very good resistance to general corrosion in sulphuric, phosphoric and acetic acid as well as to pitting and SCC.
- UNS
- N08904
- ASTM, AISI
- 904L
- EN Name
- X1NiCrMoCu25-20-5
- EN Number
- 1.4539
- ISO
- 4539-089-04-I
Powder designed for
- Additive Manufacturing (AM)
- Metal Injection Moulding (MIM)

This metal powder is manufactured by Inert Gas Atomization (IGA), producing a powder with a spherical morphology which provides good flow characteristics and high packing density.
-
Product description
Osprey® 904L is a high-alloy austenitic stainless steel characterized by very good resistance to general corrosion in sulphuric, phosphoric and acetic acid as well as very good resistance to pitting corrosion and stress corrosion cracking (SCC).
Main characteristics of Osprey® 904L
- Very good resistance to attacks in acidic environments, e.g. sulfuric, phosphoric and acetic acid
- Very good resistance to pitting in neutral chloride-bearing solutions
- Much better resistance to crevice corrosion than steels of the ASTM 304 and ASTM 316 types
- Very good resistance to stress corrosion cracking
- Good weldability
This metal powder is manufactured by Inert Gas Atomization (IGA), producing a powder with a spherical morphology which provides good flow characteristics and high packing density. In addition, the powder has a low oxygen content and low impurity levels, resulting in a metallurgically clean product with enhanced mechanical performance.
Technical data
Page updated Sep 8, 2023 9:15 AM CET (supersedes all previous editions)
-
Chemical composition (nominal), %
- Fe
- Bal.
- C
- 0.02
- Cr
- 19.0-23.0
- Ni
- 23.0-28.0
- Mo
- 4.0-5.0
- Si
- 1.0
- Mn
- 2.0
- S
- 0.035
- P
- 0.045
-
Powder characteristics and morphology
Powder for Metal Injection Moulding (MIM)
Osprey® MIM powder has a spherical morphology, resulting in high packing density. This enables the manufacture of feedstocks with high powder loading, which not only minimizes binder costs but also reduces part shrinkage during debinding and sintering. Spherical powder also has excellent flow characteristics, resulting in reduced tool wear and consistent mould filling.
Osprey® MIM powder's low oxygen content allows better control of carbon and consistency during sintering. Low oxygen levels, together with high packing density, also facilitate faster sintering.
-
Particle size distribution
Powder for Metal Injection Moulding (MIM)
Osprey® metal powder for Metal Injection Moulding (MIM) is available in a wide range of particle size distributions, from under 5 μm up to 38 μm. The table shows our standard particle size distributions for MIM powders.
Typical particle size distributions for Metal Injection Moulding (MIM)* Size (μm) D10 (μm) D50 (μm) D90 (μm) ≤ 38 5.5 13.0 31.0 ≤ 32 5.0 12.0 29.0 80% ≤ 22 4.5 11.5 27.0 90% ≤ 22 4.0 10.5 22.0 90% ≤ 16 3.5 8.0 16.0 *Particle size measurements performed using a Malvern laser particle size analyzer, typical D10, D50 and D90 provided.
Tailor-made particle size distributions are available on request. Contact us to discuss your specific requirements.
-
Mechanical properties
Test samples were made by Laser Powder Bed Fusion (L-PBF) technology, based on a GE Concept Laser M2 machine operated by Flono Additive. The testing followed the general principles defined in ISO 17296-3 covering the main characteristics and corresponding test methods for porosity, hardness, tensile and Charpy impact testing. In addition to ASTM F3122-14 - Standard Guide for Evaluating Mechanical Properties of Metal Materials Made via Additive Manufacturing Processes.
The Osprey® 904L powder used had a powder size distribution of 15 to 45 microns. The as-built samples were mechanically post processed (by turning, milling, cutting, grinding etc.) according to the standard-compliant test specimen requirements. A selection of as-built samples were heat treated (for stress relief) according to the instruction of the material type. Typically, 904L stainless steels can be solution annealing heat-treated at 1050 to 1150°C, following by rapid cooling in air or water.
Sample orientation; 90° - perpendicular to build plate (vertical).
Mechanical properties, metric units Condition Direction Yield strength Tensile strength Elongation Impact toughness Hardness Rp0.2 Rm A MPa MPa % J HRC L-PBF, as built Vertical 533 (12.5 SD) 707 (2.7 SD) 26.5 (0.7 SD) 141 (2.3 SD) 8.06 (0.11 SD) L-PBF, heat treated Vertical 406 (11.5 SD) 705 (8.1 SD) 29.2 (2.2 SD) 144 (3.5 SD) 8.66 (0.05 SD) Mechanical properties, imperial units Condition Direction Yield strength Tensile strength Elongation, % Impact toughness Hardness Rp0.2 Rm A ksi ksi % J/cm2 HRC L-PBF, as built Vertical 77.3 (1.8 SD) 103 (0.4 SD) 26.5 (0.7 SD) 176 8.06 (0.11 SD) L-PBF, as built Vertical 58.9 (1.7 SD) 102 (1.2 SD) 29.2 (2.2 SD) 180 8.66 (0.05 SD) -
Testing
All Osprey® metal powders are supplied with a certificate of analysis containing information on the chemical composition and particle size distribution. Information on other powder characteristics is available upon request.
-
Packaging
A wide range of packaging options is available, from 5kgs plastic bottles to 250kg metal drums.
5 kg (11 lbs) Plastic bottles
6 kg (13 lbs) Plastic bottles
10 kg (22 lbs) Plastic bottles
20 kg (44 lbs) Metal cans
100 kg (220 lbs) Steel drums
150 kg (330 lbs) Steel drums
250 kg (551 lbs) Steel drums
All packaging materials are suitable for air, sea and road freight.Contact us for more information and to discuss your packaging requirements.
Disclaimer: Data and recommendations are for guidance only, and the suitability of a powder for a specific process or application can be confirmed only when we know the actual conditions. Continuous development may necessitate changes in technical data without notice. This datasheet is only valid for Osprey® powder.
Range of austenitic stainless steel
Osprey® | Standards* | Fe | C | Cr | Ni | Mo | Si | Mn | S | P | Other | O | |
---|---|---|---|---|---|---|---|---|---|---|---|---|---|
1.4882 | UNS S63019 | Bal. | 0.5 | 21 | 4.5 | - | 0.3 | 9.0 | ≤0.05 | ≤0.03 | - | - |
1.4882
|
304L | UNS S30400 / S30403 | Bal. | 0.03 | 18.0-20.0 | 8.0-12.0 | - | 1.0 | 2.0 | 0.03 | 0.045 | - | - |
304L
|
310S | UNS S31008 | Bal. | 0.08 | 24.0-26.0 | 19.0-22.0 | - | 1.5 | 2.0 | 0.03 | 0.045 | - | - |
310S
|
316L | UNS S31600 / S31603 | Bal. | ≤0.03 | 16.0-18.0 | 10.0-14.0 | 2.0-3.0 | ≤1.0 | ≤2.0 | ≤0.03 | ≤0.045 | N ≤0.10 | - |
316L
|
316Ti | UNS S31635 | Bal. | 0.08 | 16.0-18.0 | 10.0-14.0 | 2.0-3.0 | 1.0 | 2.0 | - | - | Ti 0.7,N 0.25 | - |
316Ti
|
904L | UNS N08904 | Bal. | 0.02 | 19.0-23.0 | 23.0-28.0 | 4.0-5.0 | 1.0 | 2.0 | 0.035 | 0.045 | - | - | |
HK30 | JIS J92403 | Bal. | 0.25-0.35 | 23.0-27.0 | 19.0-22.0 | 0.5 | 0.75-1.75 | 1.5 | - | - | Nb 1.20-1.50 | - |
HK30
|
N-50 | UNS S20910 | Bal. | 0.03-0.05 | 20.5-22.0 | 11.7-13.0 | 2.0-2.5 | 0.2-0.6 | 4.0-5.5 | ≤0.015 | ≤0.040 | Ta ≤0.10, Ti ≤0.02, Sn ≤0.03, W ≤0.15, Cu ≤0.75 | - |
N-50
|
N-60 | UNS S21800 | Bal. | 0.1 | 16.0-18.0 | 8.0-9.0 | - | 3.5-4.5 | 7.0-9.0 | - | - | N 0.08-0.18 | - |
N-60
|
PANACEA | - | Bal. | ≤0.05 | 16.5-17.5 | ≤0.10 | 3.0-3.5 | 0.40-0.80 | 10.5-11.5 | ≤0.04 | ≤0.04 | Co ≤0.05, N 0.15-0.60, Nb ≤0.73 | <0.2 |
PANACEA
|
* Information about more standards is available in the datasheet for the respective alloy.
Get in touch with our experts in metal powder today
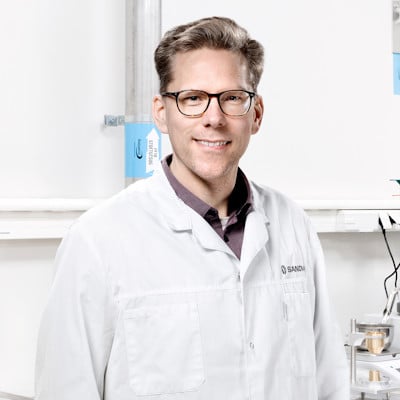