Titanium alloys
Osprey® CP-Ti (Grade 1)
Commercially pure titanium (CP-Ti) consists of 99% titanium with varying amounts of nitrogen, carbon, oxygen, iron, and hydrogen, depending on the grade.
- UNS
- R50250
- ASTM, AISI
- F67
Powder designed for
- Additive Manufacturing (AM)
- Hot Isostatic Pressing (HIP)
- Metal Injection Moulding (MIM)

This powder is manufactured by Electrode Inert Gas Atomization (EIGA), producing a powder with a spherical morphology which provides good flow characteristic and high packing density.
-
Product description
Commercially pure titanium (CP-Ti) consists of 99% titanium with varying amounts of nitrogen, carbon, oxygen, iron, and hydrogen, depending on the grade. Osprey® CP-Ti are used where high ductility combined with excellent corrosion resistance, moderate strength, and good weldability are desired. Applications are typically found in medical implants as well as for aerospace and chemical processing. Sandvik offers CP-Ti grade 1 and 2 powders in different particle sizes.
Osprey® titanium powder is manufactured to the highest international quality management standards, for example, AS9100D (aerospace) and ISO 13485:2016 (medical).
Technical data
Page updated Oct 16, 2023 1:32 PM CET (supersedes all previous editions)
-
Chemical composition (nominal), %
- Ti
- Bal.
- Fe
- ≤0.2
- O
- ≤0.18
- C
- ≤0.08
- N
- ≤0.03
- H
- ≤0.015
-
Particle size distribution
Powder for Additive Manufacturing
Osprey® metal powder for Additive Manufacturing is available in a wide range of particle size distributions that are tailored to the individual Additive Manufacturing systems. They can also be tailored to the particular requirements of the end application, both in terms of mechanical performance and surface finish.
Typical particle size distributions for Additive Manufacturing.
Typical particle size distributions for Additive Manufacturing
Process technology Size (µm) Binder jetting ≤ 16, ≤ 22, ≤ 32, ≤ 38, ≤ 45 Laser - Powder Bed Fusion (L-PBF) 15 to 53 and 10 to 45 Electron beam - Powder Bed Fusion (E-PBF) 45 to 106 Direct Energy Deposition (DED) 53 to 150 Powder for Hot Isostatic Pressing (HIP)
Osprey® powder for Hot Isostatic Pressing (HIP) is available in a broad size range, typically <250 microns, resulting in a high packing density and tap density. Low oxygen levels, together with high packing density, also facilitate faster sintering.
Powder for Metal Injection Moulding (MIM)
Osprey® metal powder for Metal Injection Moulding (MIM) is available in a wide range of particle size distributions, from under 5 μm up to 38 μm. The table shows our standard particle size distributions for MIM powders.
Typical particle size distributions for Metal Injection Moulding (MIM)*
Size (µm) D10 (µm) D50 (µm) D90 (µm) ≤ 38 5.5 13.0 31.0 ≤ 32 5.0 12.0 29.0 80% ≤ 22 4.5 11.5 27.0 90% ≤ 22 4.0 10.5 22.0 90% ≤ 16 3.5 8.0 16.0
* Particle size measurements performed using a Malvern laser particle size analyzer, typical D10, D50 and D90 provided.Tailor-made particle size distributions are available on request. Contact us to discuss your specific requirements.
-
Powder properties
Minimum powder properties values for a Laser - Powder Bed Fusion (L-PBF) cut of 15-53 µm.
Property Value Apparent density (g/cm3) ≥ 2.2 Tapped density (g/cm3) ≥ 2.5 Hall flow (s/50g) ≤ 35 -
Testing
All Osprey® metal powders are supplied with a certificate of analysis containing information on the chemical composition and particle size distribution. Information on other powder characteristics is available upon request.
-
Packaging
- 5 kg (11 lbs) CurTec plastic bottles
All packaging materials are suitable for air, sea and road freight.
Contact us for more information and to discuss your packaging requirements.
Disclaimer: Data and recommendations are for guidance only, and the suitability of a powder for a specific process or application can be confirmed only when we know the actual conditions. Continuous development may necessitate changes in technical data without notice. This datasheet is only valid for Osprey® powder.
Range of titanium alloys
Osprey® | Standards | Ti | Al | V | Fe | O | C | N | H | Y | Other, each | Other, all | |
---|---|---|---|---|---|---|---|---|---|---|---|---|---|
CP-Ti (Grade 1) | UNS R56407 | Bal. | - | - | ≤0.2 | ≤0.18 | ≤0.08 | ≤0.03 | ≤0.015 | - | - | - | |
CP-Ti (Grade 2) | UNS R56407 | Bal. | - | - | ≤0.3 | ≤0.25 | ≤0.08 | ≤0.03 | ≤0.015 | - | - | - |
CP-Ti (Grade 2)
|
Ti-6Al-4V-ELI (Grade 23) | UNS R56407 / ASTM, AISI F3001-14 | Bal. | 5.50-6.50 | 3.5-4.5 | ≤0.25 | ≤0.13 | ≤0.08 | ≤0.05 | ≤0.012 | ≤0.005 | ≤0.10 | ≤0.40 |
Ti-6Al-4V-ELI (Grade 23)
|
Get in touch with our experts in metal powder today
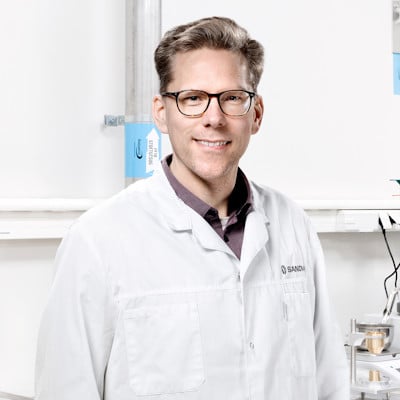