Tailor-made particle size distributions are available on request. Contact us to discuss your specific requirements.
Tool and high-speed steel
Osprey® MAR 55
Powder designed for
- Additive Manufacturing (AM)
- Cold spray
- Hot Isostatic Pressing (HIP)
- Metal Injection Moulding (MIM)
- Micro-MIM
- Sintered metal filters and foams

This metal powder is manufactured by either induction melting under Vacuum Inert Gas Atomization (VIGA) or melting under argon prior to Inert Gas Atomization (IGA).
-
Product description
Carbide-strengthened Ni-Co-Cr-Mo steels containing up to 0.4 wt.% C, along with Ni, Co, Mo, Cr, and V, were primarily designed for structural applications like large pressure vessels and hydrospace vehicles. The goal was to achieve high yield strength, wear resistance, toughness, and excellent weldability by combining carbide precipitation and Fe-Ni lath martensite concepts.
With the rise of laser-based additive manufacturing (AM) for tools with complex geometries, these steels have been revisited by Sandvik. Through computational thermodynamics, Osprey® MAR 55 was developed as an ultrahigh-strength steel offering excellent printability without the need for plate preheating, along with improved toughness, wear resistance, thermal conductivity, and oxidation resistance compared to 18Ni300 maraging steel.
Technical data
Page updated Sep 16, 2024 4:53 PM CET (supersedes all previous editions)
-
Chemical composition (nominal), %
- C
- 0.15-0.20
- N
- <0.05>0.05>
-
Powder characteristics and morphology
Powder for Additive Manufacturing
Osprey® metal powder for Additive Manufacturing is characterized by a spherical morphology and high packing density, which confer good flow properties. For powder bed processes these are essential when applying fresh powder layers to the bed to ensure uniform and consistent part build.
For blown powder processes, such as Direct Energy Deposition (DED), good flow ensures uniform build rates. Tight control of the particle size distribution also helps ensure good flowability. Low oxygen powders result in clean microstructures and low inclusion levels in the finished parts.
Powder for Hot Isostatic Pressing (HIP)
Osprey® HIP powder has a spherical morphology, resulting in high packing density. In addition, the powder has a low oxygen content and low impurity levels, resulting in a metallurgically clean product with enhanced mechanical performance.
Powder for Metal Injection Moulding (MIM)
Osprey® MIM powder has a spherical morphology, resulting in high packing density. This enables the manufacture of feedstocks with high powder loading, which not only minimizes binder costs but also reduces part shrinkage during debinding and sintering. Spherical powder also has excellent flow characteristics, resulting in reduced tool wear and consistent mould filling.
Osprey® MIM powder's low oxygen content allows better control of carbon and consistency during sintering. Low oxygen levels, together with high packing density, also facilitate faster sintering.
-
Particle size distribution
Powder for Additive Manufacturing
Osprey® metal powder for Additive Manufacturing is available in a wide range of particle size distributions that are tailored to the individual Additive Manufacturing systems. They can also be tailored to the particular requirements of the end application, both in terms of mechanical performance and surface finish.
Typical particle size distributions for Additive Manufacturing.
Typical particle size distributions for Additive Manufacturing Process technology Size (µm) Binder jetting ≤ 16, ≤ 22, ≤ 32, ≤ 38, ≤ 45 Laser - Powder Bed Fusion (L-PBF) 15 to 53 and 10 to 45 Electron beam - Powder Bed Fusion (E-PBF) 45 to 106 Direct Energy Deposition (DED) 53 to 150 Powder for Hot Isostatic Pressing (HIP)
Osprey® powder for Hot Isostatic Pressing (HIP) is available in a broad size range, typically <250 microns, resulting in a high packing density and tap density. Low oxygen levels, together with high packing density, also facilitate faster sintering.
Powder for Metal Injection Moulding (MIM)
Osprey® metal powder for Metal Injection Moulding (MIM) is available in a wide range of particle size distributions, from under 5 μm up to 38 μm. The table shows our standard particle size distributions for MIM powders.
Size (μm) D10 (μm) D50 (μm) D90 (μm) Typical particle size distributions for Metal Injection Moulding (MIM)* ≤ 38 5.5 13.0 31.0 ≤ 32 5.0 12.0 29.0 80% ≤ 22 4.5 11.5 27.0 90% ≤ 22 4.0 10.5 22.0 90% ≤ 16 3.5 8.0 16.0 - Particle size measurements performed using a Malvern laser particle size analyzer, typical D10, D50 and D90 provided.
-
Mechanical properties
Laser Powder Bed Fusion (L-PBF)
Hardness and mechanical properties in as built condition.
Build direction Ageing temperature (°C)
Ageing time
(h)Yield strength
(MPa)Tensile strength
(MPa)Elongation
(%)
Alo15Hardness
(HRC)Charpy V Notch
Impact Toughness
(J)MAR 55 (V) As built NA 1495 1630 17.9 48-49 60 MAR 55 (H) As built NA 1355 1645 16.0 48-49 60 MAR 55 (V) 480 5 1680 1870 12.0 53-54 32 MAR 55 (H) 480 5 1600 1910 10.0 53-54 32 -
Temper resistance
Hardness vs. Long time ageing at elevated temperatures.
-
Thermal conductivity
Typical thermal conductivity in as built and aged condition.
-
Wear resistance
The wear resistance of the samples was evaluated by in house chip wear tests, the severity of wear in MAR55 is significantly lower than that of 18Ni300 tested at 50±2 HRC under the same testing conditions.
-
Thermal fatigue damage
As a result of higher thermal conductivity, higher tempering and thermomechanical softening resistance, Thermal Fatigue crack propagation depth is lower than that of 18Ni300.
-
Testing
All Osprey® metal powders are supplied with a certificate of analysis containing information on the chemical composition and particle size distribution. Information on other powder characteristics is available upon request.
-
Packaging
A wide range of packaging options is available, from 5kgs plastic bottles to 250kg metal drums.
5 kg (11 lbs) Plastic bottles
6 kg (13 lbs) Plastic bottles
10 kg (22 lbs) Plastic bottles
20 kg (44 lbs) Metal cans
100 kg (220 lbs) Steel drums
150 kg (330 lbs) Steel drums
250 kg (551 lbs) Steel drums
All packaging materials are suitable for air, sea and road freight.Contact us for more information and to discuss your packaging requirements.
Range of tool and high-speed steel
Osprey® | Standards | Fe | C | Cr | Ni | Mo | Si | Mn | W | V | Co | N | |
---|---|---|---|---|---|---|---|---|---|---|---|---|---|
A6 | UNS T30106 | Bal. | 0.65-0.75 | 0.9-1.2 | 0.3 | 0.9-1.4 | 0.5 | 1.8-2.5 | - | - | - | - |
A6
|
D2 | UNS T30402 | Bal. | 1.4-1.6 | 11.0-13.0 | 0.3 | 0.7-1.2 | 0.6 | 0.6 | - | 1.1 | - | - |
D2
|
H13 | UNS T20813 | Bal. | 0.32-0.45 | 4.75-5.50 | 0.3 | 1.10-1.75 | 0.8-1.2 | 0.2-0.5 | - | 0.8-1.2 | - | - |
H13
|
HWTS 50 | - | - | 0.18-0.25 | 2.5-3.0 | - | 2.0-2.5 | 0.05-0.50 | 0.10-0.50 | - | 0.4-0.6 | - | < 0.06 |
HWTS 50
|
M2 | UNS T11302 | Bal. | 0.78-1.05 | 3.75-4.50 | 0.3 | 4.5-5.5 | 0.2-0.45 | 0.15-0.40 | 5.50-6.75 | 1.75-2.20 | - | - |
M2
|
MAR 55 | - | - | 0.15-0.20 | - | - | - | - | - | - | - | - | <0.05 | |
S2 | UNS T41902 | Bal. | 0.40-0.55 | - | 0.3 | 0.3-0.6 | 0.9-1.2 | 0.3-0.5 | - | 0.5 | - | - |
S2
|
T15 | UNS T12015 | Bal. | 1.5-1.6 | 3.75-5.00 | 0.3 | 1.0 | 0.15-0.40 | 0.15-0.40 | 11.75-13.00 | 4.5-5.25 | 4.75-5.25 | - |
T15
|
Get in touch with our experts in metal powder today
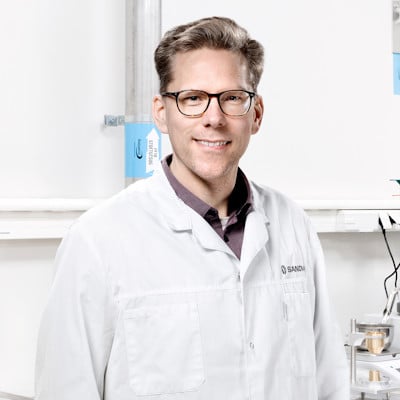